What is Incoming / Receiving Inspection?
Incoming or Receiving inspection is a critical phase in manufacturing where materials, parts, or components received from suppliers are thoroughly examined to ensure they meet the specified quality standards and requirements set by the purchasing company. It involves checking the quantity, quality, and condition of incoming goods before they are accepted into the company's inventory or production process.
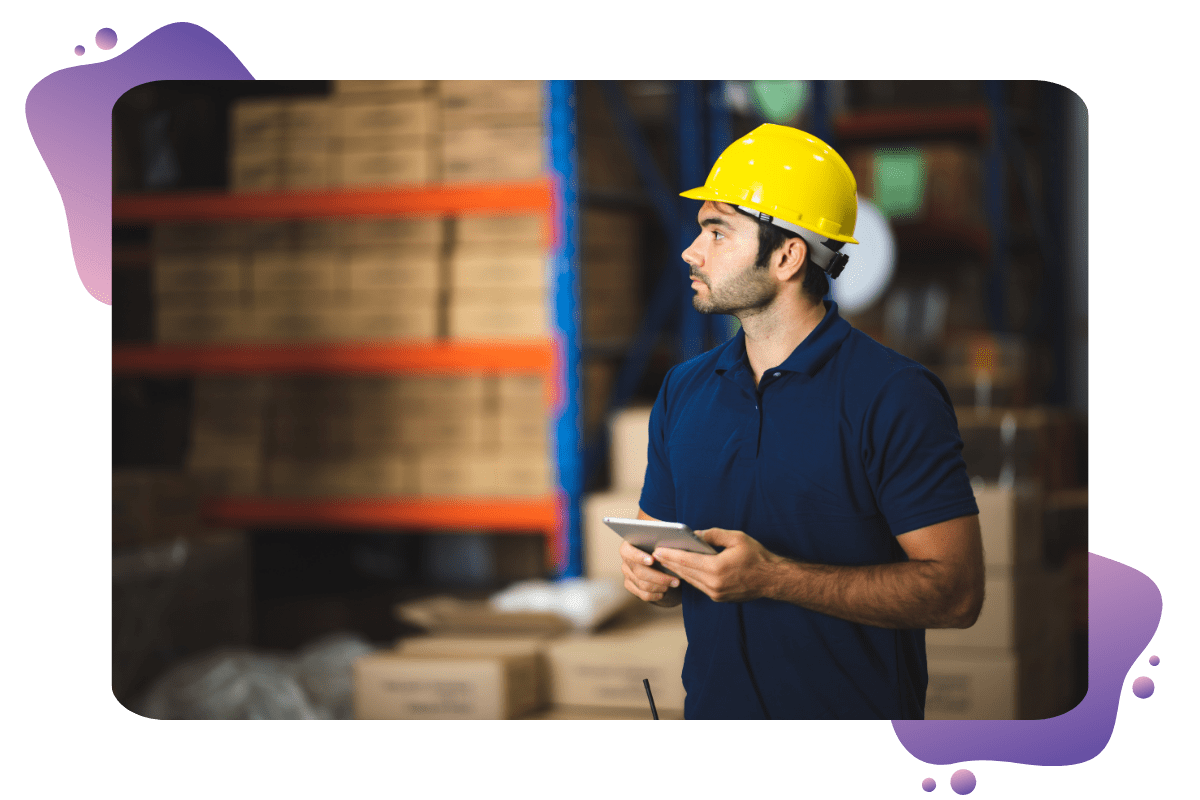
Benefits of digitizing Incoming Inspection
Benefits of digitizing Incoming Inspection
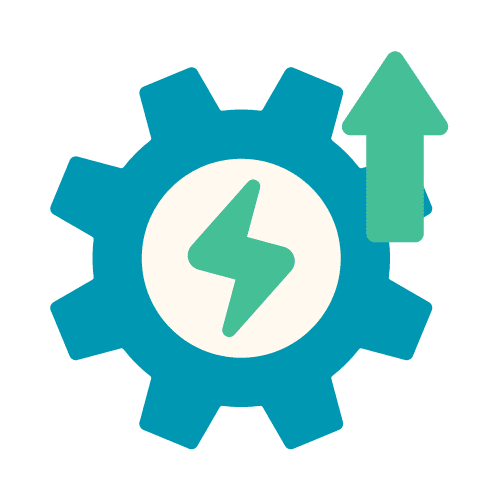
Efficiency
Digital tools streamline the inspection process, reducing manual efforts and time spent on paperwork, resulting in faster inspections.
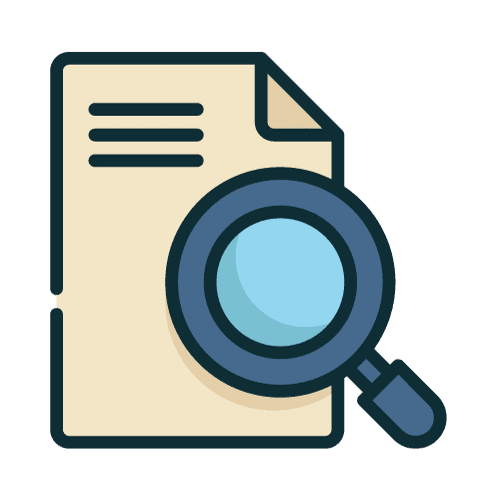
Traceability
Traceability
Traceability
Digital records enable easy tracking and retrieval of inspection data, allowing for better traceability of materials and parts.
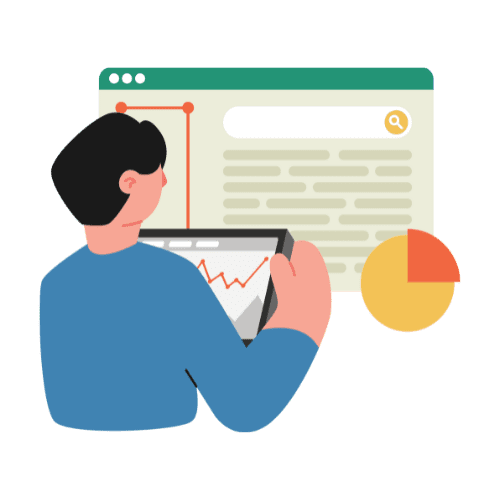
Real-time Monitoring
Digital systems often offer real-time monitoring, allowing for immediate analysis of inspection results and faster decision-making.
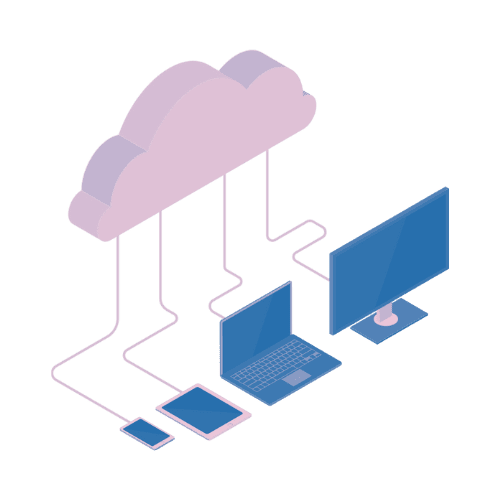
Remote Access
Remote Access
Remote Access
Cloud-based systems enable access to inspection data from anywhere, facilitating collaboration among teams and remote inspections.
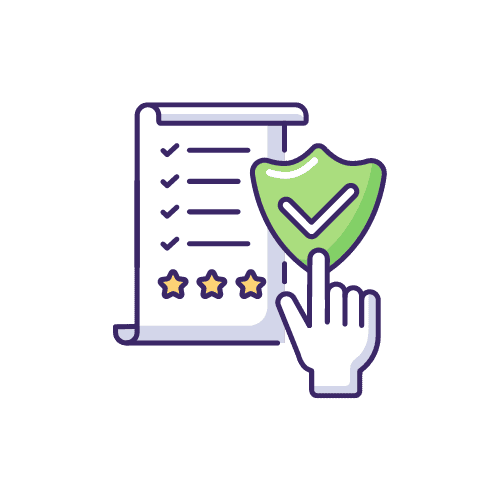
Compliance
Compliance
Digitization also helps in adhering to industry standards and regulatory requirements, ensuring proper documentation and compliance.
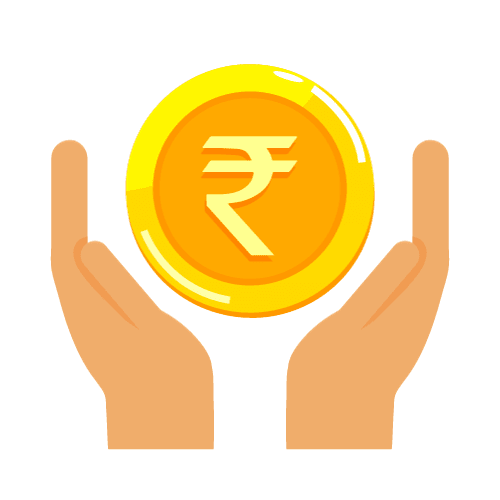
Cost Reduction
By minimizing manual efforts and errors, digitization can potentially reduce operational costs associated with inspection processes.
Key Features
- Accessible seamlessly anywhere on PC / Mobile / Tablet.
- Define your own Inspection Plans.
- Supports AQL based sampling.
- Add Users with Roles.
- Add Suppliers.
- Add Parts and define checkpoints (Visual / Dimensional).
- Add Part Image / Drawings / Inspection SOPs.
- ‘Bulk Upload’ data for quick setup.
- Check multiple samples in one go.
- Ability to attach PO and GRN / MRN.
- Validation to ensure no checkpoint is missed.
- Click images for defective parts.
- Add Remarks and place E-Signatures.
- Automatic Email with PDF reports on submission.
- Complete Inspection results in PDF with Images.
- Defective Material / Non-conformance Report.
- Quality Incharge Approval with Remarks.
- Key Supplier KPIs: Lead Time, Defect Rate, Accepted / Rejected Lots, Average Inspection Score etc.
Digitally Transform Incoming Inspection Process
Digitally Transform Incoming Inspection Process
Create Inspection Plan
Define Inspection Plan based on 3 criteria:
- AQL (Acceptable Quality Limit): Define lot size and sample size for ‘Reduced’, ‘Normal’ and ‘Tighten’ inspections. Set Acceptance Number for Critical / Major / Minor defects.
- Passing %: Define sample size along with passing percentage to define lot result. Ex: Sample Size - 10, Passing % - 80% (8 Parts).
- Characteristic Class: Set % for Critical / Major / Minor checkpoints for lot result. Ex: Critical - 100%, Major - 80%, Minor - 60%.
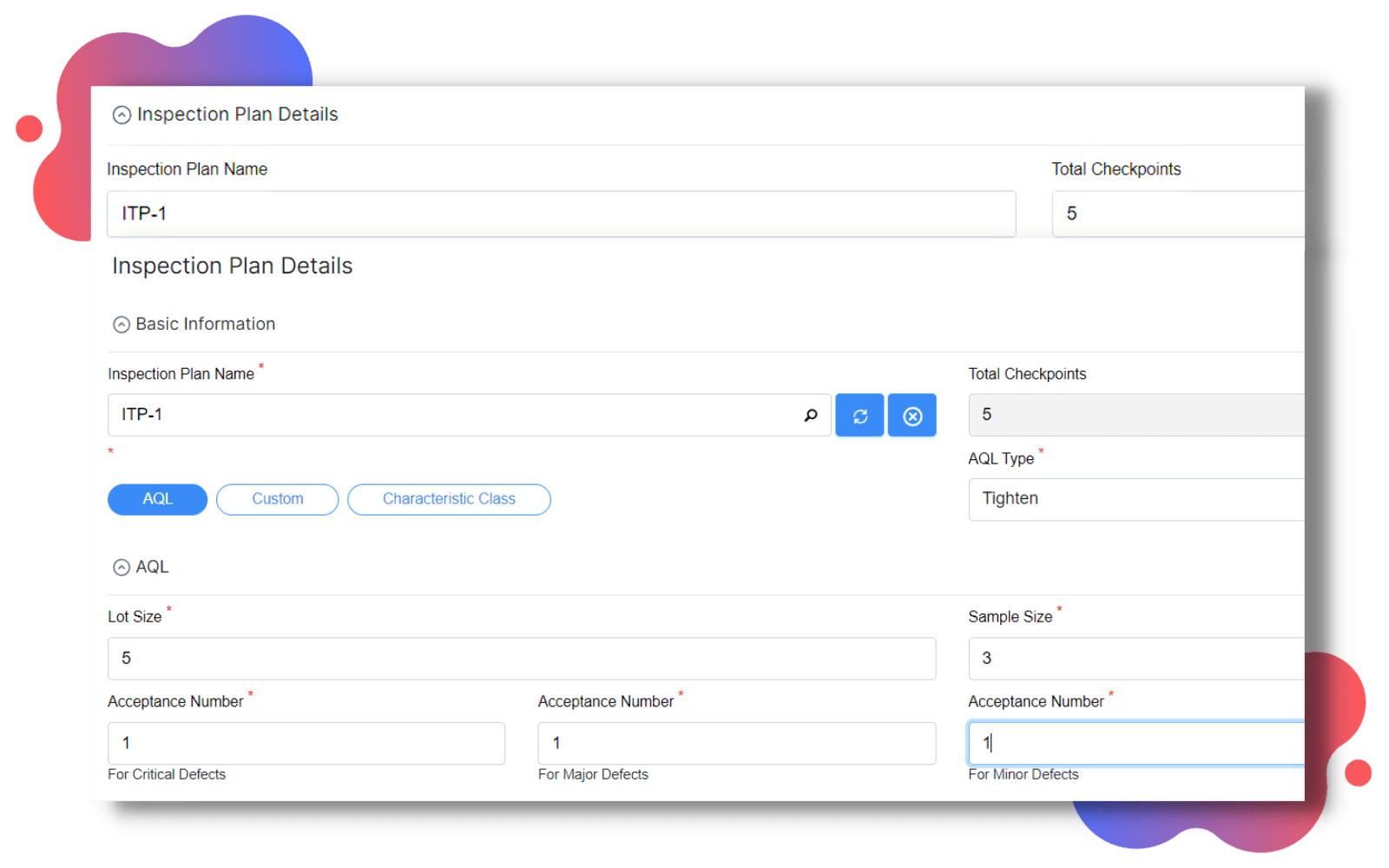
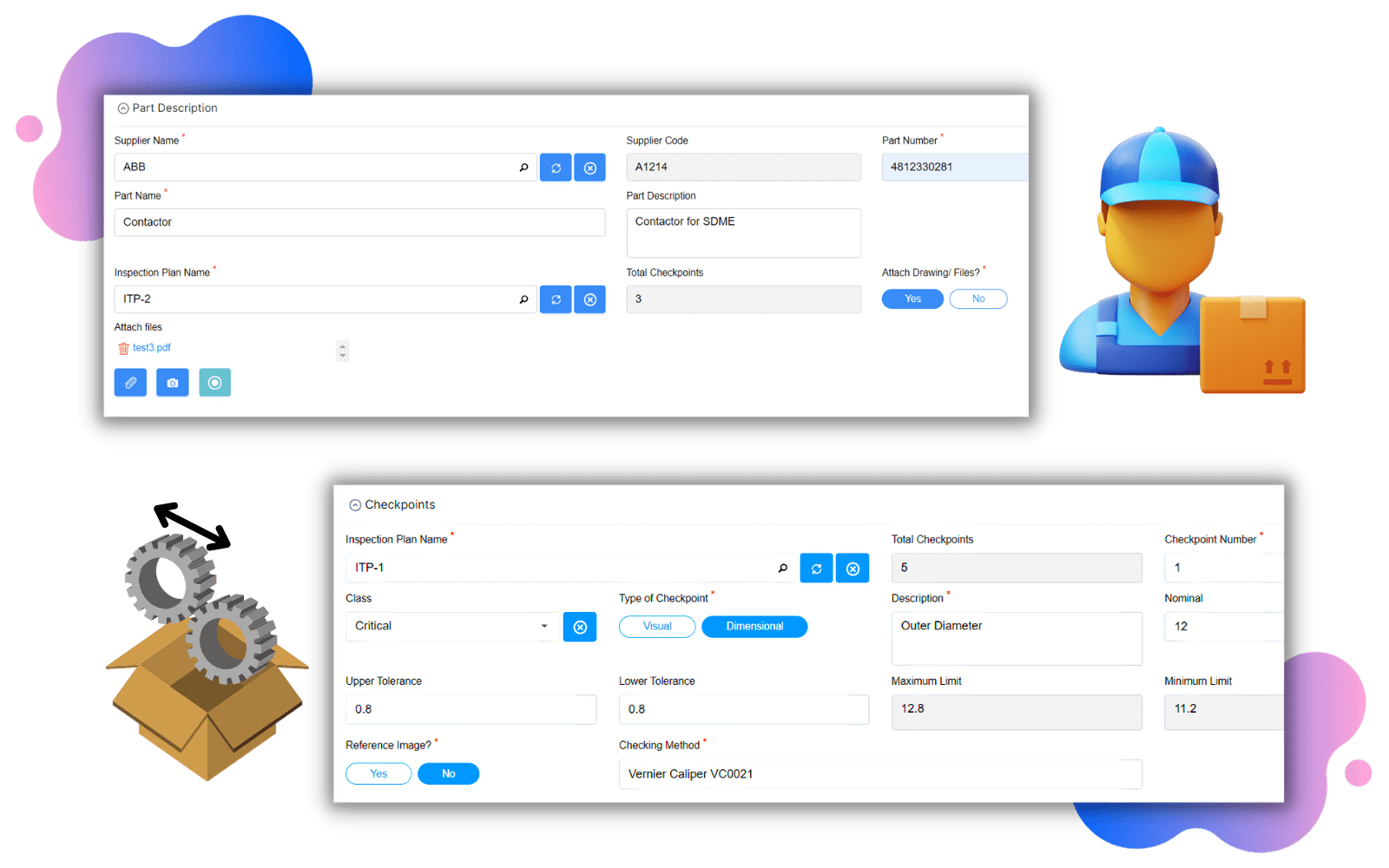
Add Suppliers, Parts and Checkpoints
Add Suppliers, Parts and Checkpoints
- Add Users with predefined roles like ‘Inspector’ and ‘Quality Incharge’.
- Add Suppliers along with their contact information.
- Add Parts and link them with existing Suppliers.
- Add Reference Images, Part Drawings, Inspection SOPs to assist the quality inspector during inspection.
- Define Checkpoints for parts (Visual or Dimensional) along with ‘Checking Method’.
- Bulk Upload the data from Excel to accelerate your early setup process.
Auto ‘Switching Rules’ as per ISO-2859
Auto ‘Switching Rules’ as per ISO-2859
Ensure supplier quality by applying ‘Switching Rules’ automatically. ‘Sample Size’ automatically detected based on current status of supplier (Normal / Reduced / Tighten).
- Normal to Reduced: 10 consecutive lots accepted.
- Normal to Tighten: 2 of last ‘5’ or fewer lots rejected.
- Tighten to Normal: 5 consecutive lots accepted.
- Reduced to Normal: 1 lot rejected.
- Tighten to Inspection Discontinued: 5 lots rejected.
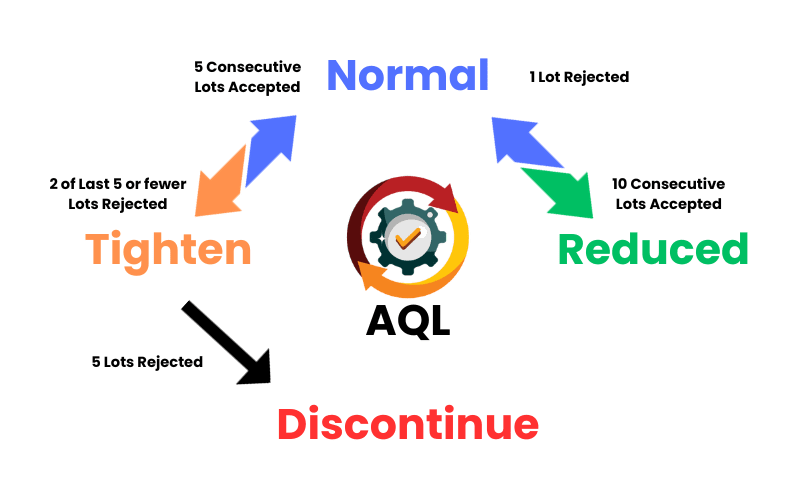
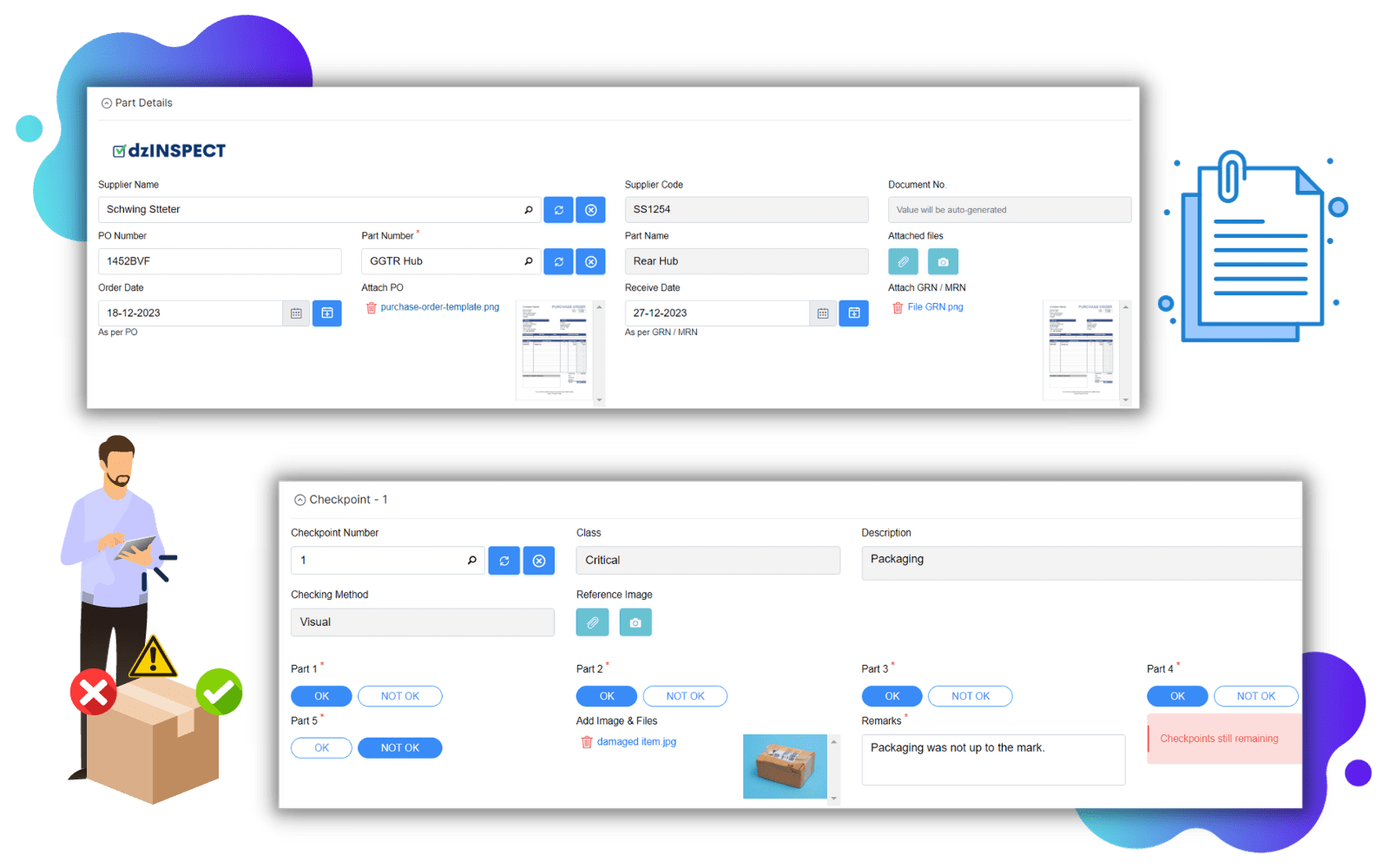
Perform Inspection on PC / Mobile / Tablet
Perform Inspection on PC / Mobile / Tablet
Inspection needs to be carried out once the material is received by ‘Receiving Department’ and segregated properly in warehouse for Inspection by Quality team. Inspections can be easily carried out on your PC / Mobile / Tablet.
- Ease of access during remote inspections.
- Select Supplier and Part.
- Attach PO (Purchase Order), if available.
- Attach GRN / MRN (Good Received / Material Receipt Note).
- Automatic ‘Sample Size’ detection based on AQL or as per Inspection Plan.
- Check multiple samples for a checkpoint.
- Verify all the parameters / checkpoints associated with the part.
- Add ‘Images’ for defective parts along with ‘Remarks’.
Robust Reports and Real-time Analytics
Robust Reports and Real-time Analytics
Get automatic PDF reports on email. Verify the inspection results and Approve/ Reject the lot along with remarks. Monitor supplier KPIs and trends in real-time dashboard.
- Automatic Email reports to Quality In-charge.
- Inspection Results with attached PO and GRN.
- Provision for E-Signatures.
- DMR / NCR (Defective Material / Non-conformance Report) for defective lots.
- Supplier KPIs include: Lead Time, Defect Rate, Accepted / Rejected Lots.
- Average time taken by Inspector to carry out Inspection.
- Average Inspection Score.
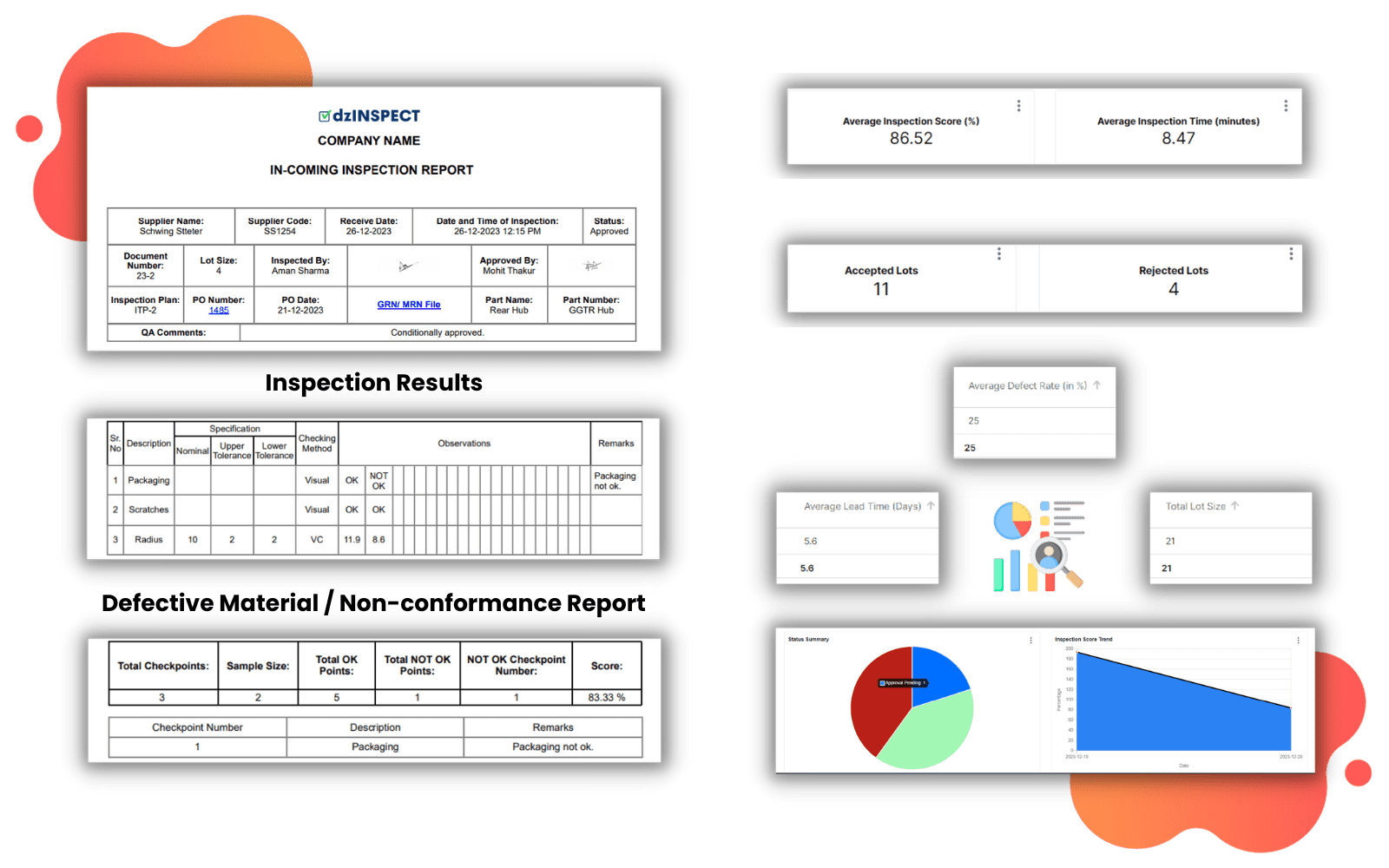
Contact Us
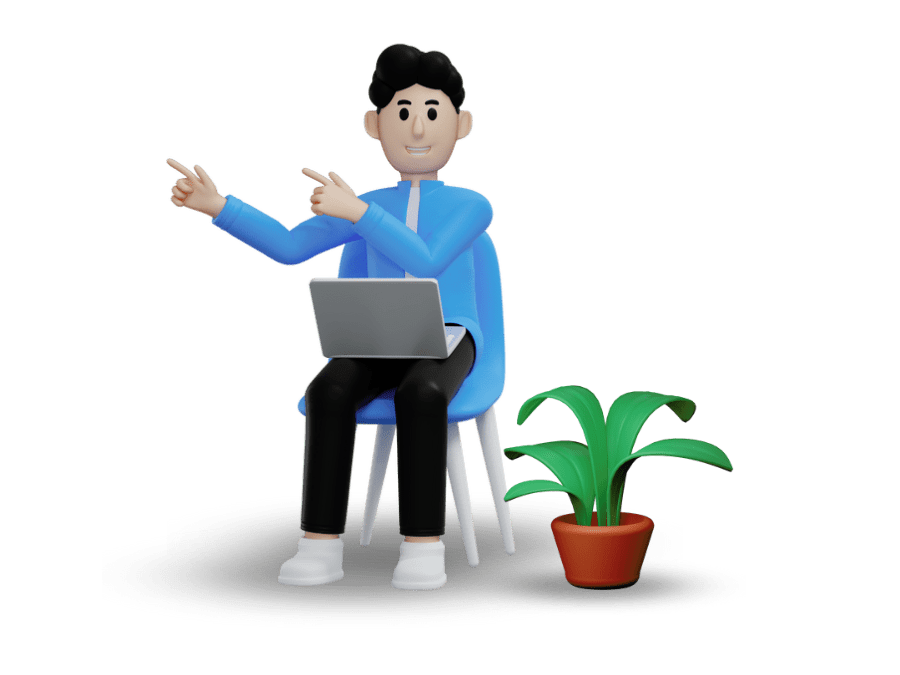