What is Pre-Delivery Inspection?
Pre-delivery inspection, also known as Outgoing or Pre-Dispatch Inspection is a quality control process that occurs before a product is delivered to ensure it meets specified standards. By carefully examining each part, manufacturers can find and fix any problems, making sure only products that meet the quality standards are sent out for delivery. This helps manufacturers keep a good reputation and build trust with their customers.
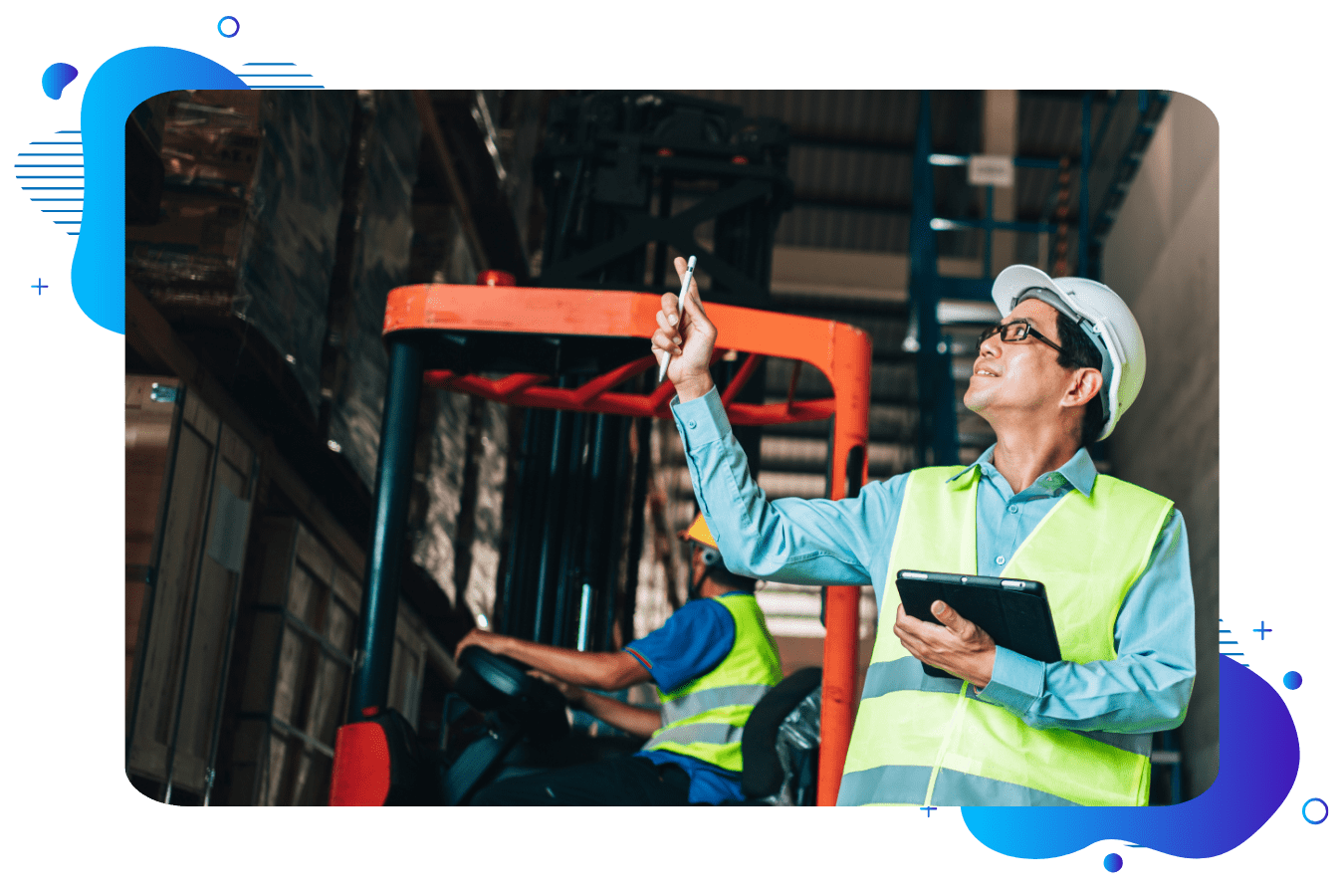
Benefits of Digitizing Pre-Delivery Inspection
Benefits of Digitizing Pre-Delivery Inspection
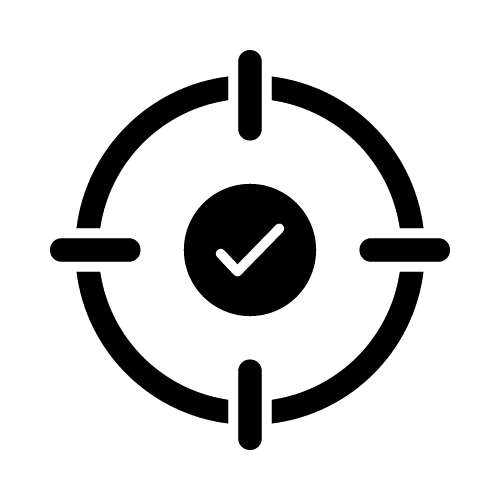
Enhanced Accuracy
Enhanced Accuracy
Digitizing pre-delivery inspection processes reduces the likelihood of human errors, ensuring more accurate and reliable results.
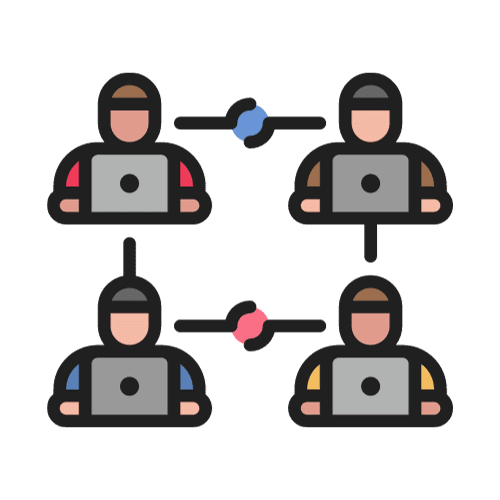
Better Communication
Digital platforms enable seamless communication between different departments involved in the inspection process with the help of automatic emails with inspection reports.
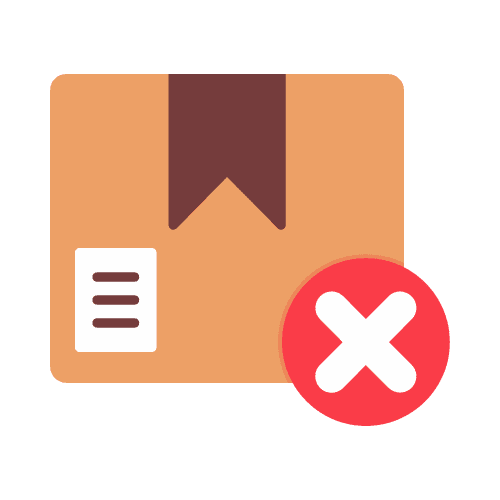
Reduced Reworks
Reduced Reworks
Digital systems allow you to identify defective parts in real time and help you take corrective actions. This helps in reducing rejections and recalls from customer end.
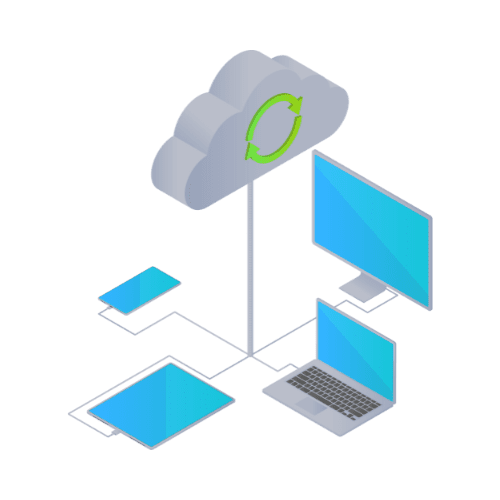
Remote Access
Remote Access
Remote Access
Cloud-based systems enable access to inspection data from anywhere, facilitating collaboration among teams and remote inspections.
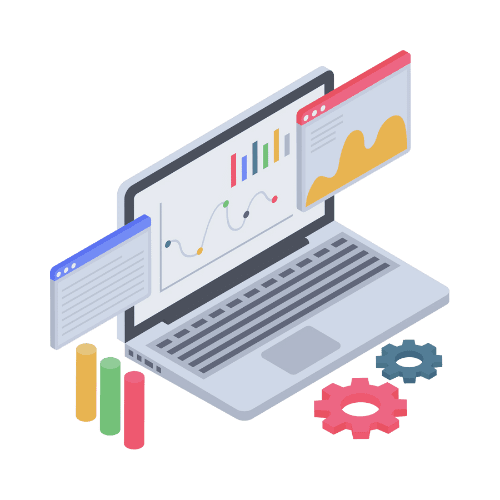
Data Analytics
Digitized inspection data can be used to identify patterns, trends, and areas for improvement, contributing to continuous enhancement of product quality and processes.
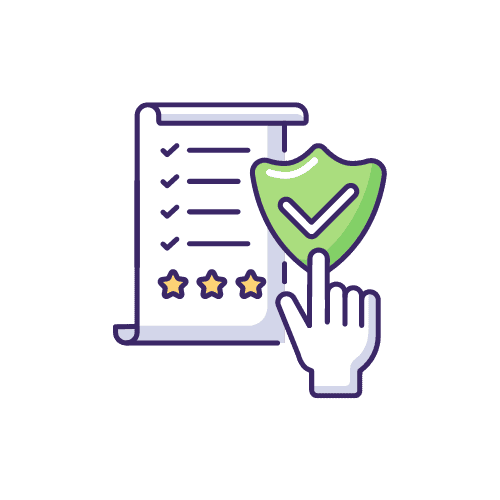
Compliance
Compliance
Digitization also helps in adhering to industry standards and regulatory requirements, ensuring proper documentation and compliance.
Key Features
- Accessible seamlessly anywhere on PC / Mobile / Tablet.
- Define your own Inspection Plans.
- Supports AQL based sampling.
- Add Users with Roles.
- Add Customers and Parts.
- Define Checkpoints (Visual / Dimensional).
- Add Part Image / Drawings / Inspection SOPs.
- ‘Bulk Upload’ data for quick setup.
- Check multiple samples in one go.
- Define quantity of rework and replace parts.
- Validation to ensure no checkpoint is missed.
- Add images for defective parts with Remarks.
- E-Signatures.
- Automatic Email with PDF reports on submission.
- Complete Inspection results in PDF with Images.
- Defective Material / Non-conformance Report.
- Quality Incharge Approval with Remarks.
- KPIs like Average Defect Rate, Average Rework Rate, Total Accepted / Rejected lots etc.
Gateway for Digitized Pre-Delivery Inspections
Gateway for Digitized Pre-Delivery Inspections
Create Inspection Plan
Define Inspection Plan based on 3 criteria:
- AQL (Acceptable Quality Limit): Define lot size and sample size. Set Acceptance Number for Critical / Major / Minor defects.
- Passing %: Define sample size along with passing percentage to define lot result. Ex: Sample Size - 10, Passing % - 80% (8 Parts).
- Characteristic Class: Set % for Critical / Major / Minor checkpoints for lot result. Ex: Critical - 100%, Major - 80%, Minor - 60%.
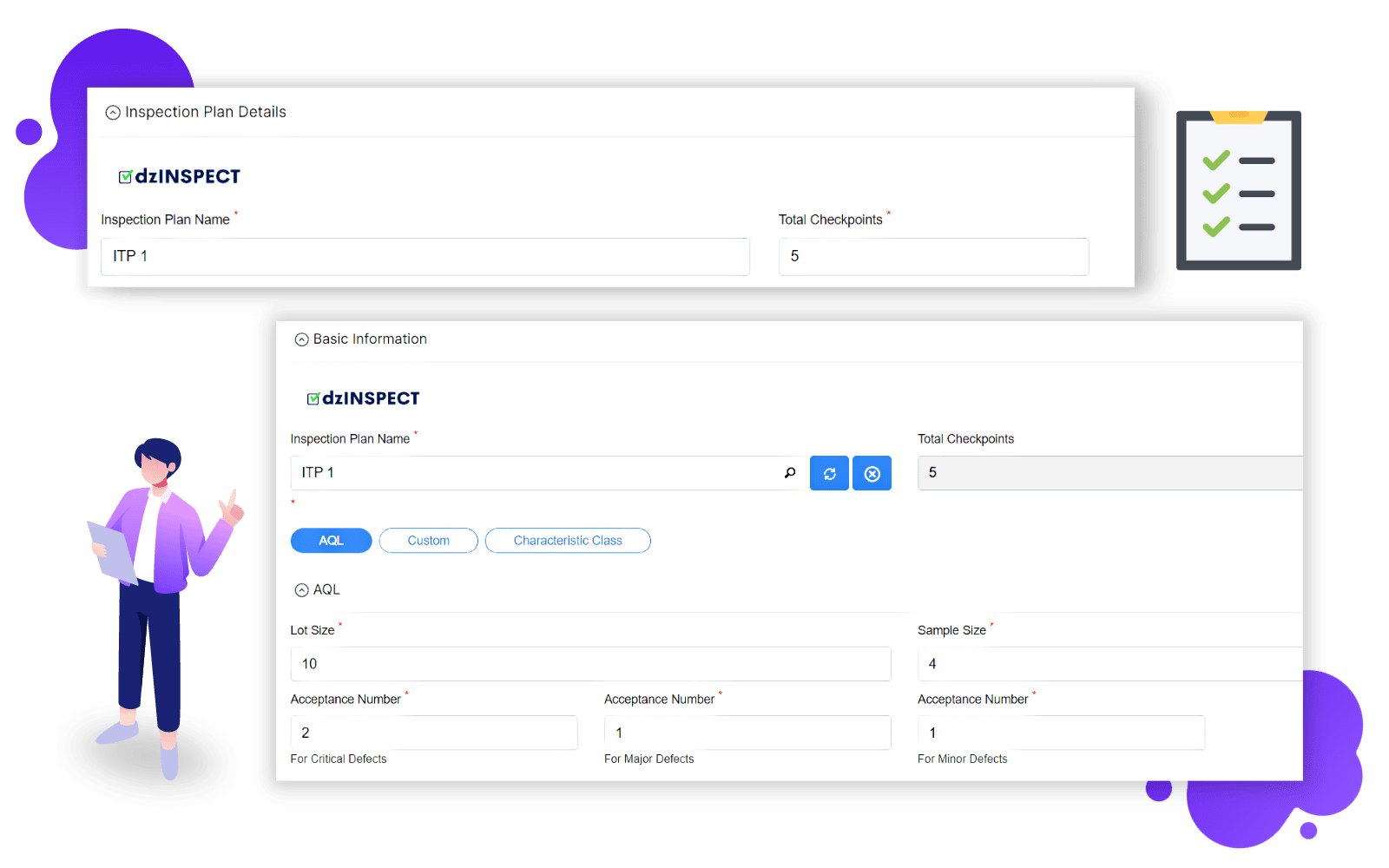
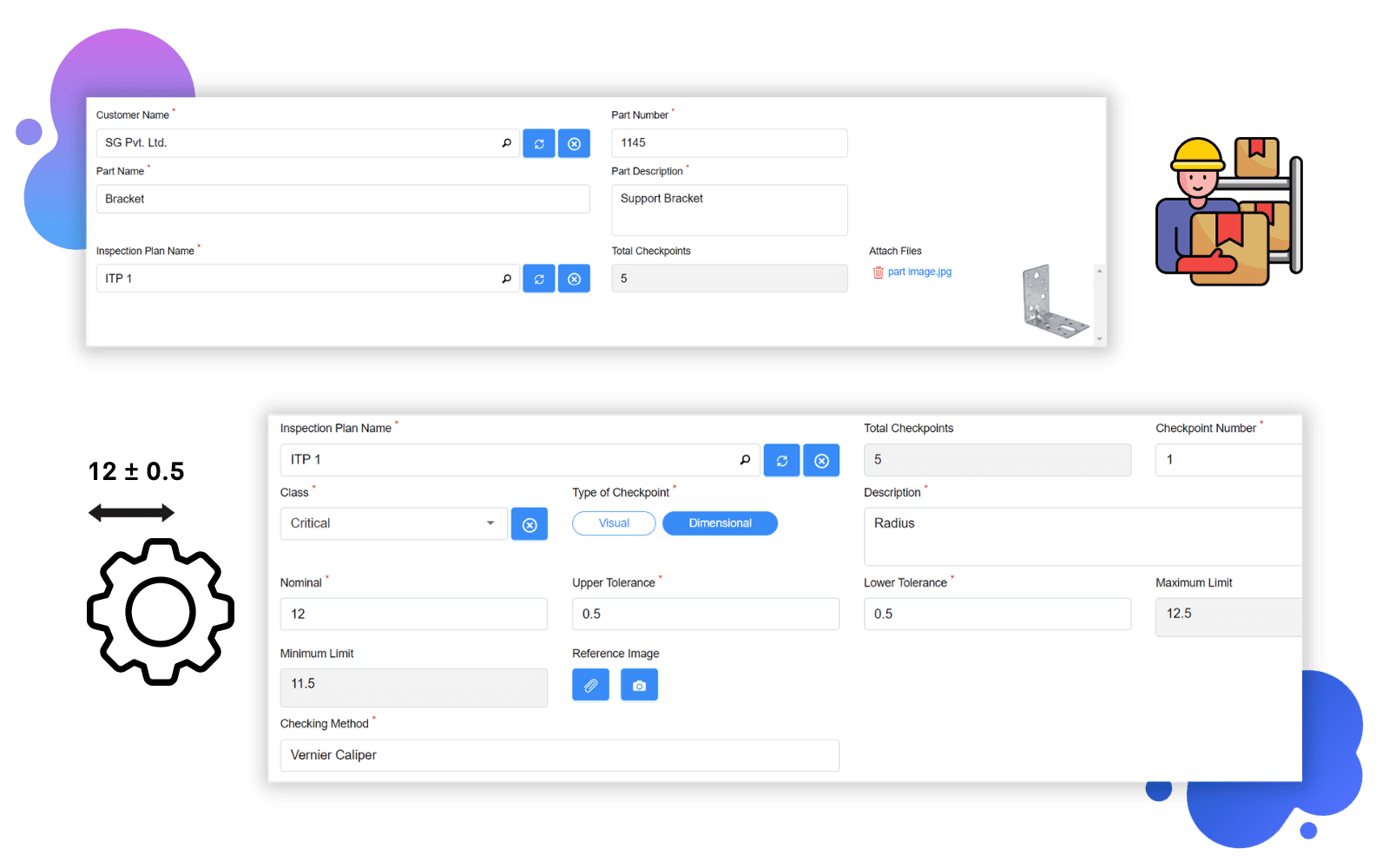
Add Customers, Parts and Checkpoints
Add Customers, Parts and Checkpoints
- Add Users with predefined roles like ‘Inspector’ and ‘Quality Incharge’.
- Add Customers along with their contact information.
- Add Parts and link them with existing Customers.
- Add Reference Images, Part Drawings, Inspection SOPs to assist the quality inspector during inspection.
- Define Checkpoints for parts (Visual or Dimensional) along with ‘Checking Method’.
- Bulk Upload the data from Excel to accelerate your early setup process.
Detect Critical, Major, and Minor Defects
Detect Critical, Major, and Minor Defects
Define critical, major and minor checkpoints for parts. System will automatically count the number of critical, major and minor defects found during inspection and compare it with the actual 'acceptance number' defined in AQL.
Critical Defects:
- Immediate attention is required for defects that could halt essential product functionalities or pose significant safety risks.
Major Defects:
- Issues that, while not causing a complete product failure, significantly impact core functionalities.
Minor Defects:
- Superficial problems that don't affect functionality or user experience.
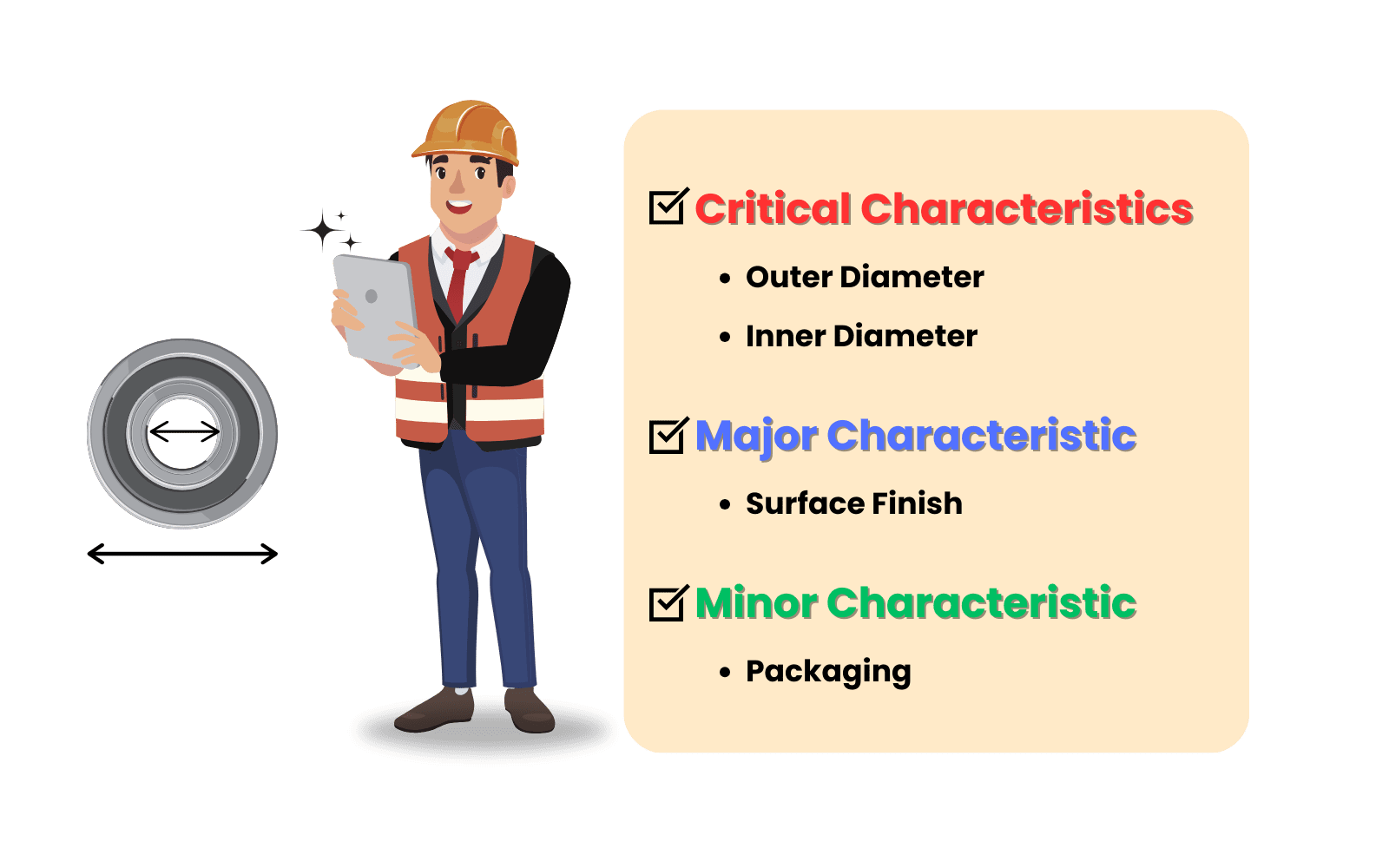
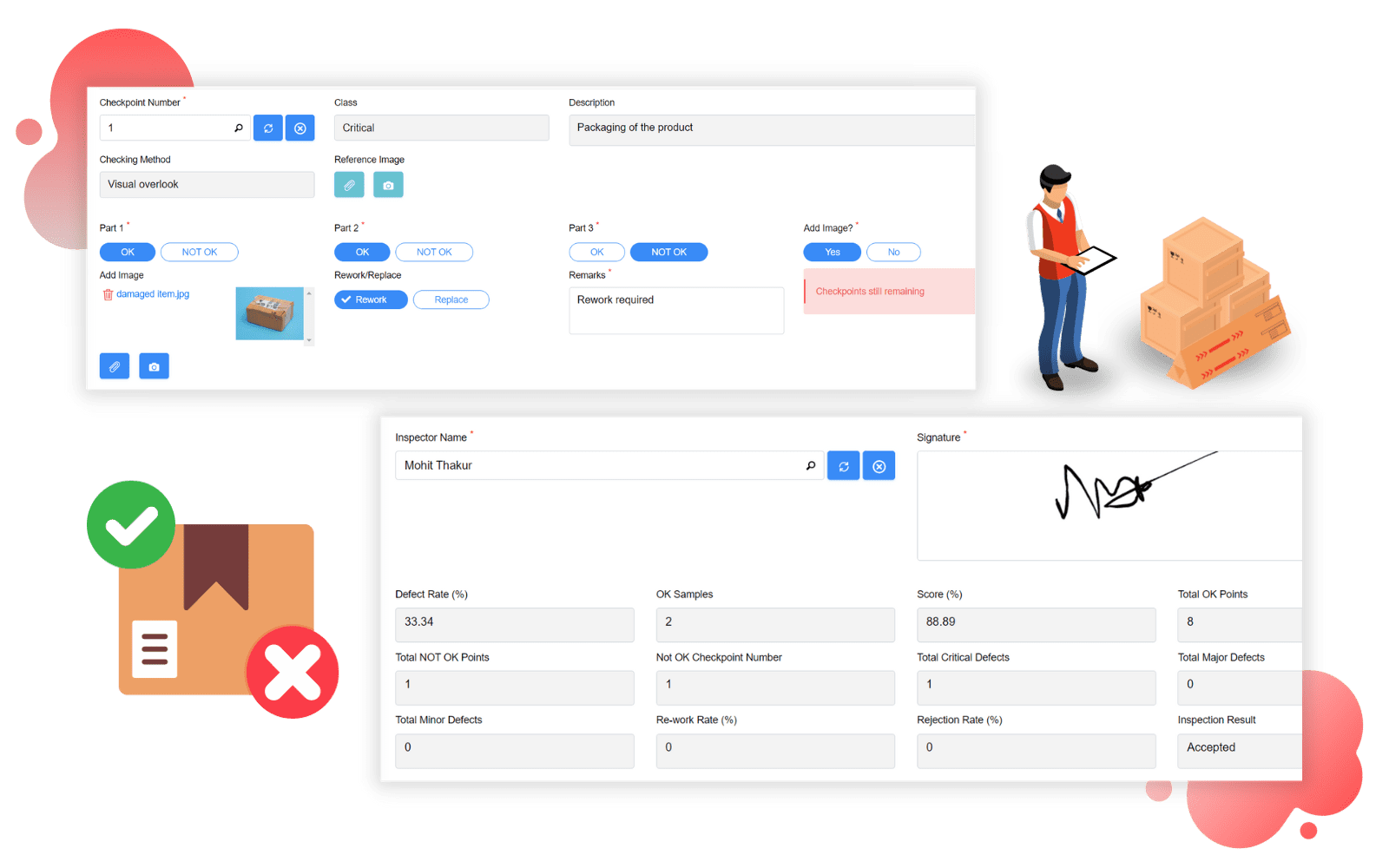
Perform Remote Inspection on PC / Mobile / Tablet
Perform Remote Inspection on PC / Mobile / Tablet
Perform inspection on mobile, tablet or a PC with all the inspection related information at your fingertips. Ensure customer satisfaction and trust by verifying critical parameters and making sure that only good quality products are delivered with no defects.
- Ease of access during remote inspections.
- Select Customer and Part.
- Automatic ‘Sample Size’ detection based on AQL or as per Inspection Plan.
- Check multiple samples for a checkpoint.
- Verify all the parameters / checkpoints associated with the part.
- Add ‘Images’ for defective parts along with ‘Remarks’.
Automatic Reporting and Real-time Dashboards
Automatic Reporting and Real-time Dashboards
Get automatic PDF reports on email. Verify the inspection results and Approve/ Reject the lot along with remarks. Monitor KPIs and trends in real-time dashboard.
- Automatic Email reports to Quality Incharge.
- Inspection Results with Rework and Replace Quantity.
- Provision for E-Signatures.
- DMR / NCR (Defective Material / Non-conformance Report) for defective lots.
- KPIs include: Defect Rate, Rework Rate, Rejection Rate, Accepted / Rejected Lots etc.
- Average time taken by Inspector to carry out Inspection.
- Average Inspection Score.
- Perform Pre-Delivery Inspection and share your results to your customers to establish confidence in your operational procedures.
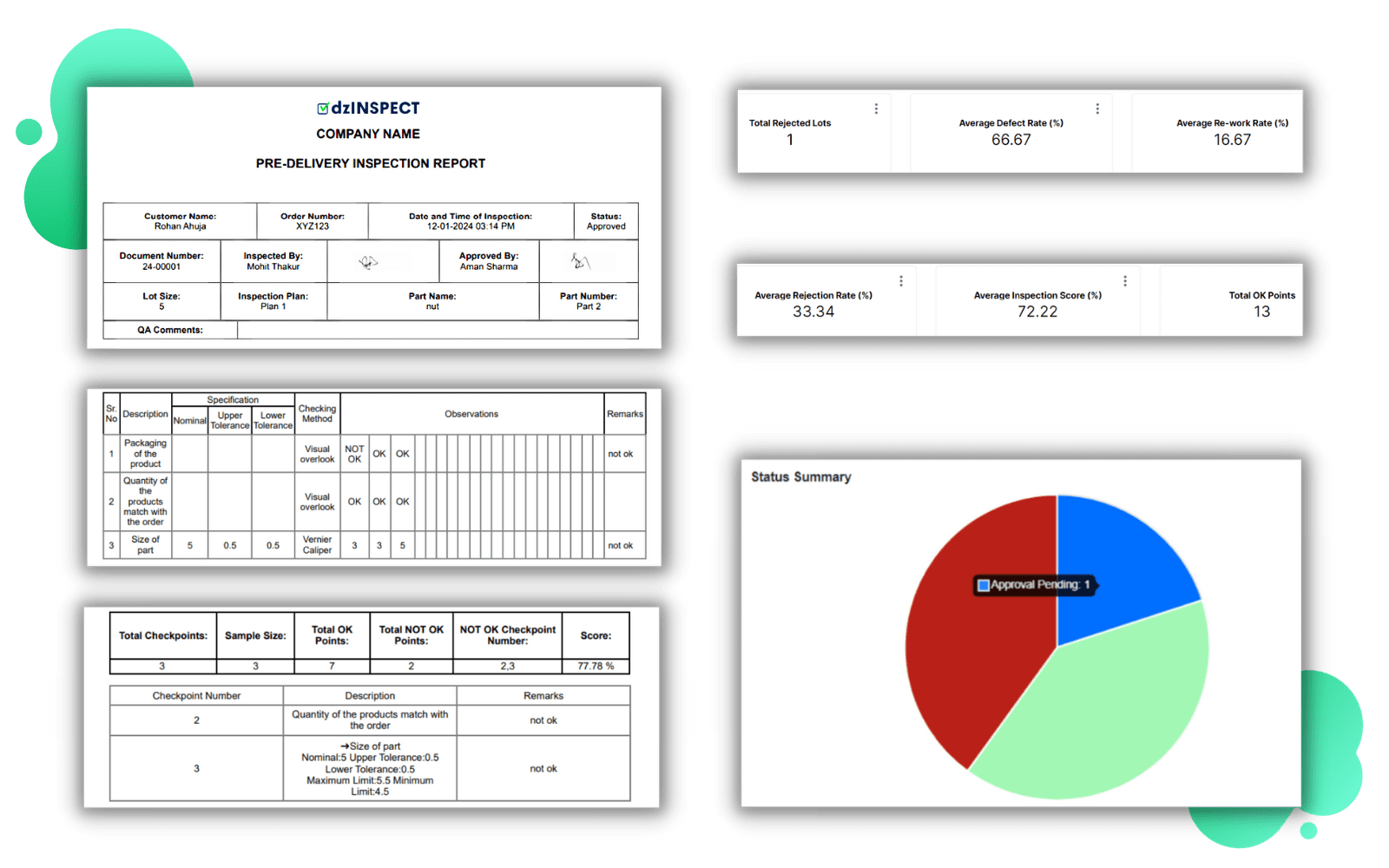
Contact Us
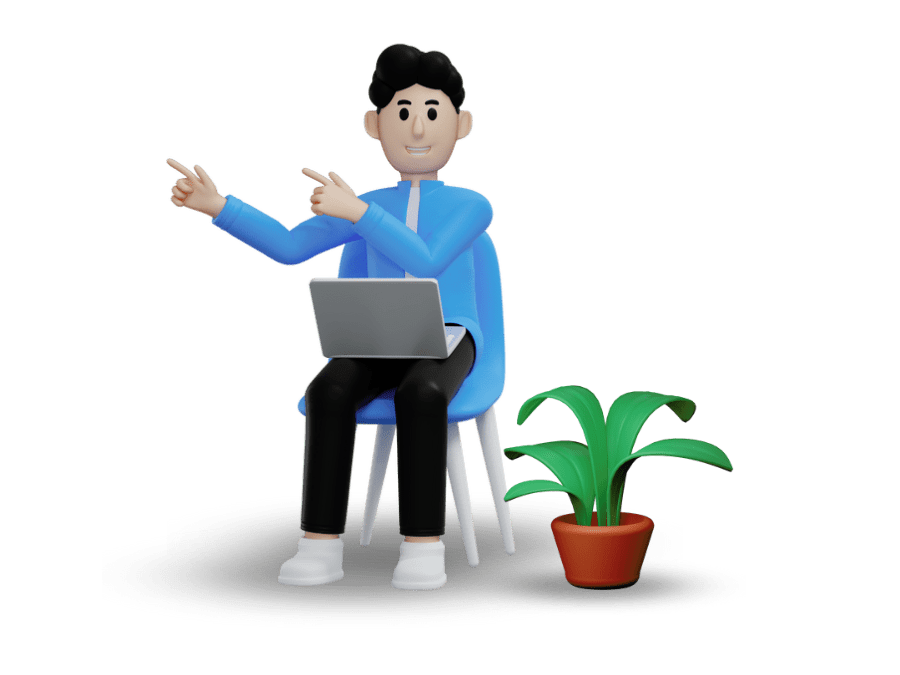